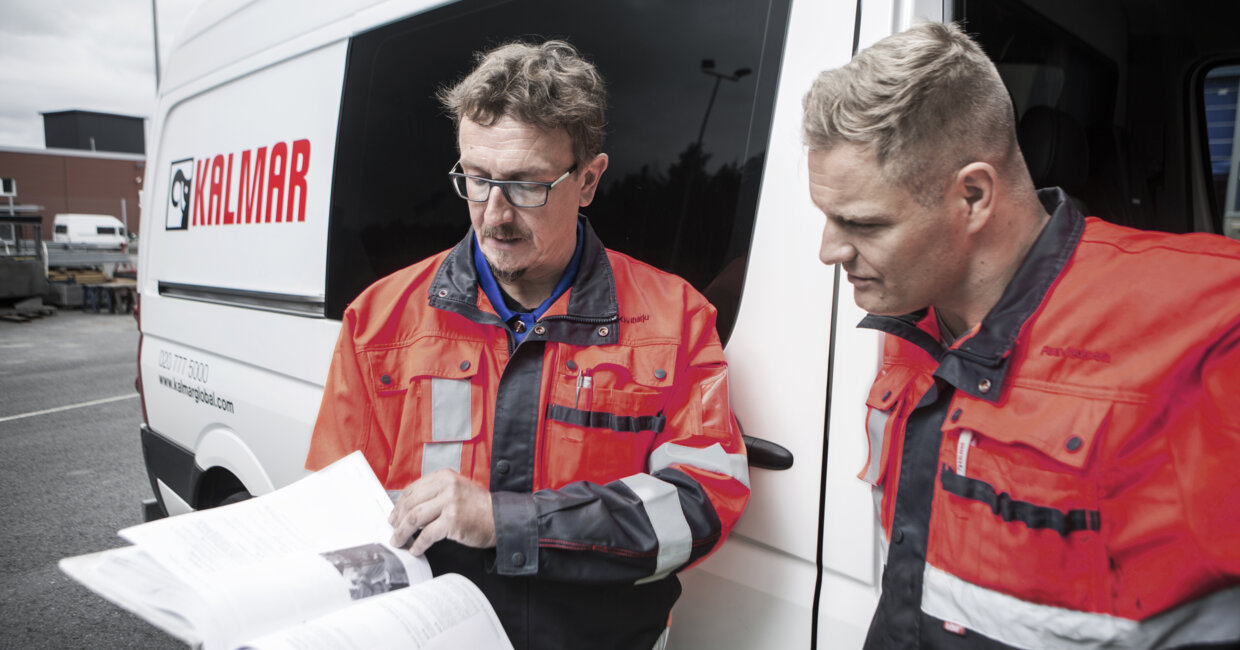
A comprehensive approach to optimum maintenance
Equipment issues can be resolved before they arise if a fleet is able to communicate automatically with its maintenance team. This is already possible today, and it will become even more common in the future. Kalmar is prepared for the rapid coming changes.
Admittedly, the idea of preventive maintenance is brilliant, but it’s not a new idea. Maintenance checks have been scheduled based on operating time or mileage for quite some time. It is, however, safe to say that preventive maintenance is undergoing a radical transformation, starting with how data are gathered.
“We fit all our new mobile equipment with connectivity hardware. This means that forklift trucks and other machines can send data automatically to a cloud app while they are operating,” says Timo Elo, Sales Manager at Kalmar Services. According to Elo, automatic data collection will help maintenance staff schedule service based on real-time data and respond to problems even before they arise -- and could become acute.
“It will be easier than ever to plan maintenance and schedule maintenance work as to have minimal impact on customer operations.”
Elo points out that connectivity hardware can also be retro-fitted to existing Kalmar equipment, and even to other manufacturers’ equipment, so that the entire fleet can be managed with the same system.
“Connectivity has been possible for a while already, but it’s only recently that it has become clearly cost-effective.”
Preventive maintenance is undergoing a radical transformation, starting with how data are gathered.
Time-based to condition-based maintenance
The typical data collected from equipment include the number of moves and running hours. They offer very useful information, but why not collect more, and more varied data, at the same time? Teemu Tapio, who manages contracts at Kalmar Services, agrees. He looks daily at a future where preventive maintenance becomes predictive maintenance. In the predictive mode, maintenance tasks will be based on the condition of the equipment rather than the run time.
“For example, data on temperature and battery consumption may indicate a drag on the brakes. Or, data on location and vibration could point to a pothole on the route that would in time shorten the lifespan of the machine,” Tapio says.
The good news is that all of this data can already be collected by the newest Kalmar equipment.
Kalmar Insight – overview of the entire fleet
Whatever data are collected may prove invaluable to various users – but only if they have easy access to it.
“The performance management tool, Kalmar Insight, offers an overview of the use and condition of the fleet in the terminal or the industrial plant. It presents real-time data on each piece of equipment,” Elo says. He thinks Kalmar Insight will boost both maintenance and operations.
“All equipment can be tracked, and past events can be played back visually when searching for bottlenecks in the operation.”
Digital tools boost Kalmar services and customer operations
When a terminal or industrial plant outsources fleet maintenance to Kalmar, equipment data will be analysed by Kalmar’s maintenance staff.
“Actually, our internal maintenance management system offers possibilities for automatic analyses that trigger alerts and service notifications. These will then be processed by our back office staff who will decide on the best plan of action,” Tapio says.
When a service order is scheduled, the maintenance management system produces a list of needed spare parts. Afterwards, when the maintenance technician ticks off the completed job on his mobile app, the system will automatically update the service plan for that specific machine.
“Our customers can view these service plans on their own Kalmar Insight tools, where they can also make service notifications and monitor maintenance actions,” Tapio adds.
Elo expects that internal process development at Kalmar will make a notable difference to customers.
“Digital tools enable us to provide fast and high-quality maintenance services and thus help our customers increase their fleet availability and operational performance,” Elo says.
“Our main goal is to help our customers optimise their operations while we make sure their fleet is maintained at peak performance and operating at all times."
Looking into the future of a fleet
Tapio finds it challenging to differentiate between existing and future maintenance concepts as new features arise constantly and customers adopt them at different times.
“What I know for sure is that Kalmar maintenance services continue to develop fast and they will definitely look different even a year from now.”
Tapio says the massive flow of data will offer new ways to predict the future of a fleet and to optimise a fleet to a specific type of operations to extend its life span, enhance performance and generate greater cost-efficiency. “We are constantly learning more about how collected data reflects the use and surroundings of the equipment. Visualisation of the data opens up opportunities to identify, for example, bottlenecks in the operations and take corrective action.”
In the end, the data will help Kalmar deliver both better maintenance and more durable and efficient machines.
“Our main goal is to help our customers optimise their operations while we make sure their fleet is maintained at peak performance and operating at all times,” Elo says.
Related articles
Further reading
Subscribe and receive updates in your email
Assine nossas publicações