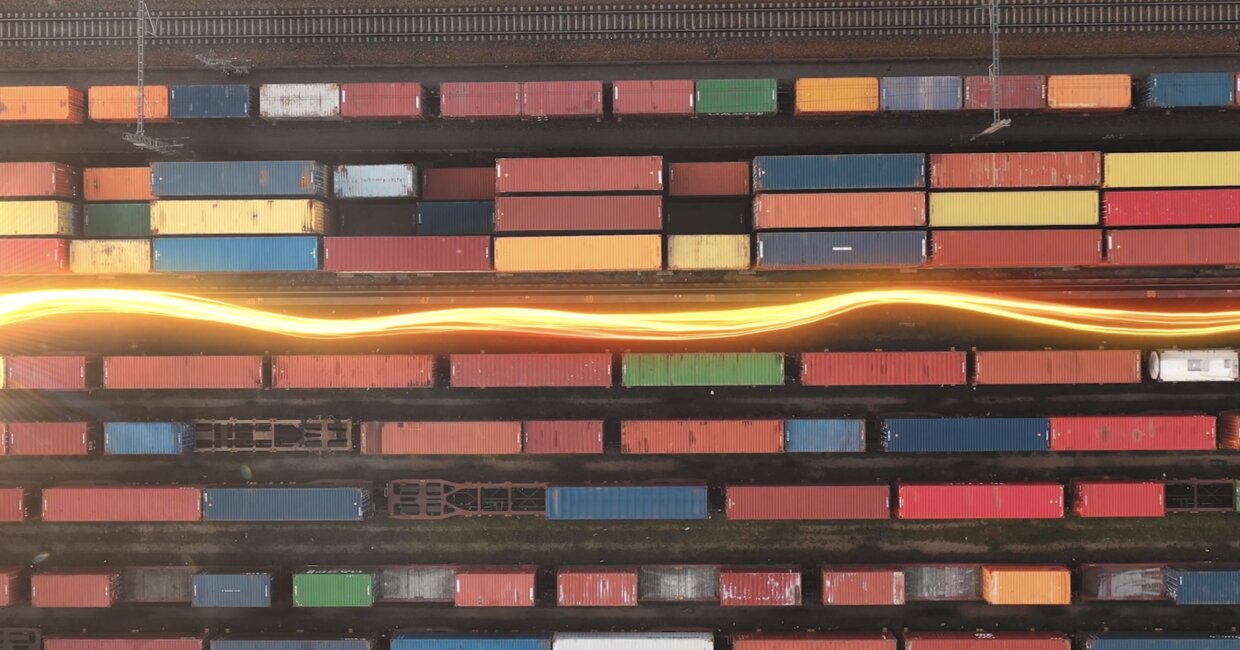
Automation gaining ground in rail intermodal terminals
With the increasing pressure to reduce congestion around terminals and improve the environmental performance of logistics value chains, intermodal transport is a booming business across Europe and the US. Intermodal terminals provide a vital link between larger hubs like seaports, and the key to their success is maximising capacity and throughput – safely, efficiently and intelligently. Three of our leading experts take a closer look at the drivers and challenges in the EU and US markets – and how automation technologies can help operators to take the next big steps forward.
The intermodal transport networks in Europe and the US are both dominated by rail, with the European system covering close to 222,000 km of track, with 12,000 cargo yards spread across 30 countries mostly operated by small and medium-sized players. The network in the US covers close to 228,000 km and is dominated by seven independent Class 1 railroad operators. The heart of this huge network in North America is the Midwest Great Lakes region, which from a railroad perspective is the central hub between the east and west coasts and the gulf of Mexico.
Shifting volumes away from the road
Intermodal traffic in Europe comprises a variety of cargo types beyond standard sea containers, including semi-trailers and tanktainers. In the US, anything and everything you can think of is handled by rail intermodal: trailers, international and domestic 53' containers, medical supplies, grain, fertilizers, food and more.
“US rail intermodal volumes dwarf those in Europe, with trains often exceeding 1.5 km in length and carrying containers in a double-stack configuration. But the drivers for growth are the same: the need for cost reductions and legislative pressure to reduce carbon emissions,” says Thomas Graef, Intermodal Sales Manager, Kalmar Automation Solutions.
In the US, rail intermodal essentially means transporting international and domestic containers and trailers to and from ports, rail yards and distribution centres. “Inland port connections are on the rise in this market too,” Graef explains. “These are critical points that facilitate the speedy movement of cargo from marine vessels to on-dock rail and out into the interior of the country.”
In Europe these inland connections are often located along the continent’s extensive inland waterway system, which has an important role to play in intermodal cargo transportation. Kalmar’s dedicated solutions for this market address operators of all shapes and sizes, from large seaports with on-dock intermodal terminals to small and medium-sized inland terminals.
Operators seeking proven, reliable solutions
“Europe is a flexible and diverse market that’s really only at the beginning of its automation journey,” explains Uwe Pietryga, Sales Director, Kalmar Automation Solutions. “This is primarily because compared to large seaports, the many smaller and medium-sized operators lack the capability to invest in solutions. Nonetheless, there are ongoing projects that feature automated equipment like remotely operated RMGs and dedicated horizontal transport equipment like automated guided vehicles (AGVs) or straddle carriers,” he continues.
In the US, automation will become more and more important as the industry looks to improve safety by reducing the need for people to work in close proximity to each other and to heavy machinery. It will also be a critical driver to attract the next generation of workers. “Some of the bigger players in the market are already acting as early adopters and this trend will continue,” says Graef. “From a manufacturer’s perspective the key will be to manage expectations and ensure that the benefits are clear for all to see,” he continues.
Regardless of geographical location, in terms of automation intermodal operators are seeking proven, reliable solutions that are low risk and offer a quick return on investment. This is where standardisation with concepts like the Kalmar One automation system can help.
Small steps, big benefits
With automation it pays to have a structured approach to implementation, and Kalmar is well placed to support intermodal operators in this regard. “Putting the right foundations in place is key to ensuring success, and our Terminal Design Services Team can help operators to clarify their needs and identify the right combination of automation solutions and equipment to address them,” says Jarno Kuipers, Senior Manager, Terminal Development, Kalmar. “The result is a low-risk setup based on proven technologies that deliver optimal performance.”
“It’s also important to remember that automation does not by default mean an entirely autonomous operation where people are removed from the equation,” points out Kuipers. “There are degrees of automation and the distance that an operator travels along this road will depend on their needs and level of readiness.”
The adoption of automation will certainly increase in the intermodal market, but the complexity will be determined on a case-by-case basis. “As a trusted partner, our role is to help customers make the link between the investment and the benefits they can realise, and to drive home the message that the adoption of automation can happen at a pace they are comfortable with,” Pietryga highlights.
RMGs and RTGs are a common site at intermodal terminals, and several operators in Europe, particularly on-dock rail terminals, are already moving towards remote operation in order to increase safety and cut costs. In common with the US, intermodal operators also view automation as a way to attract future generations to the industry with innovative technologies and a more comfortable working environment.
Helping intermodal operators get the most from their terminals
The key to success in intermodal operations is maximising capacity and throughput within the available space, and this requires the optimal combination of eco-efficient equipment, intelligent services and expert support. Whether a customer is constructing a greenfield terminal or wants to adjust the setup of a brownfield site, Kalmar’s Terminal Design Services team can provide expert support from the early planning stages to ensure the best possible results.
The team has an enviable track record, with hundreds of successful projects under its belt. “To give an example, we’ve helped intermodal operators to increase stacking density and extend rail buffer capacity by adopting straddle carriers instead of terminal tractors or road trucks to transport containers to and from wide-span cranes,” explains Kuipers.
In addition to capacity and throughput, eco-efficiency is another important driver in intermodal transport and often goes hand in hand with automation. Kalmar is a world leader in this regard, with solutions that help customers to do more with less – reducing fuel consumption and emissions, optimising cargo flows and cutting overall operational costs.
Working hand in hand with customers every step of the way
Kalmar’s approach to working with intermodal operators is based on knowledge and competences built up from decades of experience working with intermodal operators of all kinds. “Our solution-sales approach keeps us fully focused on developing a system that’s tailored to the customers’ needs, yet based on proven standardised technologies,” Pietryga emphasises. “Our solutions are also scalable and open to enable smooth integration with third-party offerings and backed by lifetime support,” he concludes.
“Flexibility is important in this market because while overall operating concepts can be replicated relatively easily, individual operators have specific needs that can only be addressed through close cooperation and solid planning up front,” Kuipers explains.
“It is also important to remember that moving from manual to semi-automated operations represents a significant investment in terms of systems and equipment, particularly for smaller operators,” Graef points out. “Our job as a supplier is to maintain an open dialogue with customers and work on developing cost-efficient and easily deployable solutions that can help them ramp up their level of automation at a comfortable pace.”
Related articles
Further reading
Customer case
Subscribe and receive updates in your email
Assine nossas publicações