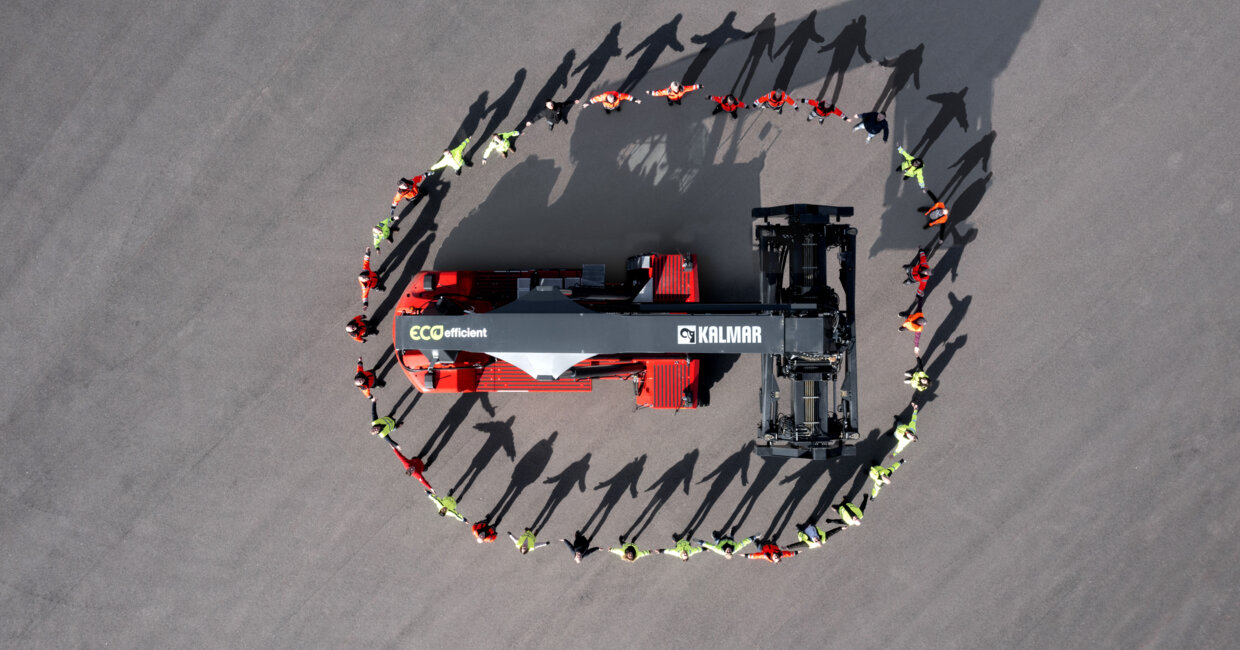
Teamwork powers zero emission machine innovation
Kalmar's electric reachstacker development team hit the high notes.
The introduction of Kalmar’s first electric reachstacker represents a major advance in the development of environmentally friendly cargo handling equipment. It is also testimony to the many hours the team behind the creation of the machine have put into its development.
By any measure the project to develop the first zero emissions reachstacker has been a resounding success. Through effective and efficient teamwork we are now able to offer our customers a more sustainable solution for their daily operations. But what are the key elements of effective teamwork?
Beating any challenge
Perhaps the most important element is the ability to overcome challenges – and the electric reachstacker development team have demonstrated their ability to problem solve by continuing to interact efficiently during an unprecedented global pandemic.
“The most difficult challenge we faced during the project was meeting deadlines while working from home,” says project manager Erik Johansson. “But this was also the best part in that as a team we managed to deliver even though we were faced with so many obstacles.”
A team working like a symphony
When we think of what makes a great team we can perhaps equate it to an orchestra - where each member must focus on their own task while working with all the other members to create the best possible overall result.
“The teamwork has been extremely efficient,” says Mette Kjems Baerentzen, product portfolio manager for the electric reachstacker project. “Bi-weekly meetings with updates on all major aspects of the project ensured that everyone was kept informed of developments at all times and most importantly that nothing was overlooked in each project member’s areas of responsibility.”
Mette believes that the open, clear and to-the-point communication maintained throughout the project contributed to a highly cooperative, structured and motivating working process.
“This approach minimised the time spent on coordinating project meetings and gave everyone an overview of the project’s status at all times as well as an insight into each project section’s needs, requirements and challenges,” adds Mette. “This made it easier for the rest of the team to offer help or advice.”
Project activities were spread out across the organisation and most of the people involved in project-related tasks were undertaking these tasks in additional to their regular responsibilities explains Carina Wigren, project manager services.
“These colleagues were always willing to go the extra mile in order to support the project in the best possible way,” she says.
The interest is rising
Customer reaction to Kalmar’s first electric reachstacker suggests all this hard work has paid off. Interest in the machine continues to rise with more than 40 meetings already conducted - including visits to Ljungby Innovation Center in Sweden to test drive the machine organised by the counterbalanced container handling (CCH) division in coordination with the sales teams. Many more such meetings are planned for the coming weeks and months.
One machine has already been sold and two field test machines are scheduled for delivery. These customers will soon be able to appreciate at first hand the result of the enormous effort made by our electric reachstacker project team.
Marketing Manager CCH
Related articles
Further reading
Subscribe and receive updates in your email
Assine nossas publicações